EIB Funds PulPac’s Scalable Alternative to Single-Use Plastics
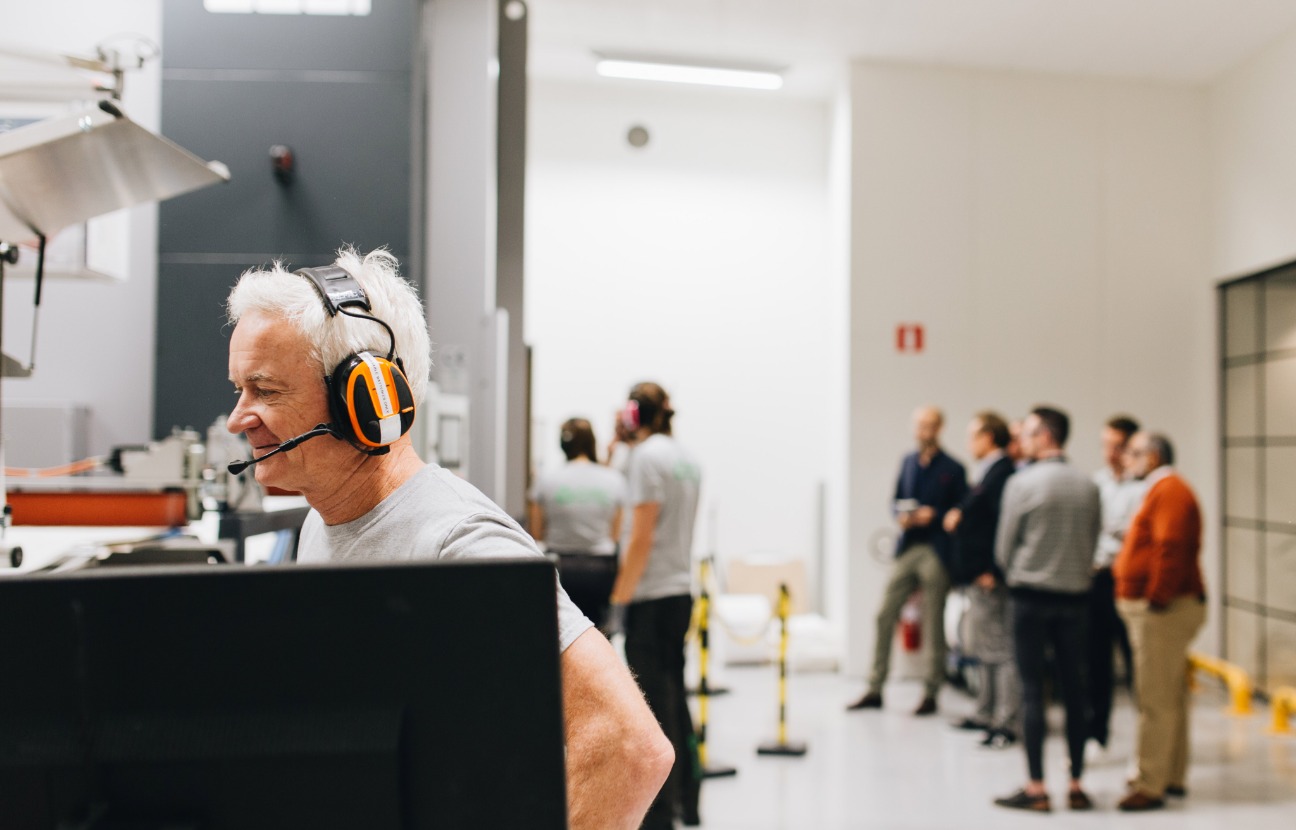
Image: Dry Molded Fiber technology demonstrated at PulPac’s innovation center in Gothenburg
Gothenburg-based packaging innovator PulPac has secured €20 million in venture debt funding from the European Investment Bank (EIB) to scale up its patented Dry Molded Fiber technology. The financing comes under the EU’s InvestEU programme, aimed at driving the green transition by supporting industrial innovation, sustainability, and economic resilience.
The funding will support PulPac’s R&D and commercialization efforts between 2025 and 2029, accelerating the global rollout of its unique fiber-based packaging solution. Target applications include rigid packaging for coffee cup lids, cutlery, pharmaceutical packaging, fashion hangers, and even bottles—products traditionally made from single-use plastics.
MoveTheNeedle.news spoke with Roderick Sundell, CFO at PulPac, about the impact of the EIB investment.
“The funding is a catalyst for faster rollout – supporting R&D, cost reduction, and partner enablement,” he said.
A Dry Alternative to Wet Molding
PulPac’s patented Dry Molded Fiber process represents a step-change in fiber-based packaging. Unlike traditional wet molding, which mixes fiber with large amounts of water and requires long drying times, PulPac’s process is entirely dry. This makes it up to ten times faster, significantly less energy-intensive, and far more scalable.
“Our mission is to make sustainable packaging scalable and accessible,” Sundell explains.
The technology converts renewable cellulose fiber—such as pulp from trees or recycled paper—into rigid packaging without the use of water. Instead, the fibers are mechanically formed and pressed in dry form, enabling high-speed, high-volume production on industrial lines.
“Our process uses no water, less energy, and has much better cost-performance than wet molded fiber,” says Sundell. “It can compete on price, not just on sustainability merits.”
The Problem With Wet Molded Fiber
Traditional wet molding has been around for decades and is commonly used to produce fiber trays, egg cartons, and some disposable tableware. However, its limitations are becoming more apparent in the face of rising demand for sustainable packaging:
- Water usage: Wet molding is water-intensive, which makes it environmentally and economically inefficient.
- Energy consumption: Drying the water from the pulp mixture is highly energy-consuming.
- Production speed: The slow process restricts scalability and limits competitiveness with plastic.
- Sourcing and shipping: Many wet molded products are manufactured in Asia, contributing to emissions and limiting circularity in European markets.
By contrast, Dry Molded Fiber enables localized production, reduces carbon emissions, and aligns well with Europe’s waste management and recycling infrastructure.
“Dry Molded Fiber can save up to 80% in CO₂ compared to conventional molded fiber and also shows clear benefits over plastics,” says Sundell. “It fits into existing paper recycling streams in most countries, making it a strong candidate for circular packaging.”
Local Recycling, Global Impact
The fact that it fits into existing paper recycling infrastructure is a a major benefit of PulPac’s process. Unlike bioplastics, which often require separate processing, or composite packaging that’s hard to separate, Dry Molded Fiber is easy to recycle in most countries' paper waste streams. That makes it appealing for brand owners who want to deliver on their ESG promises without creating logistical headaches for retailers or consumers.
The technology also supports onshoring of packaging production, reducing transport emissions and improving resilience. As European businesses seek to de-risk global supply chains, localized sustainable packaging could become a powerful differentiator.
PulPac’s Licensing-Based Growth Strategy
PulPac doesn’t plan to become a packaging giant itself. Instead, it licenses its patented technology to converters and brands who want to produce fiber-based alternatives to plastic packaging.
“Revenue comes from licenses, bundled machine-tooling systems, and platform support,” explains Sundell. “The model scales globally through partnerships with leading players across the value chain.”
This “impact-at-scale” approach allows the technology to be deployed quickly and widely—critical when considering the EU’s environmental deadlines and bans on single-use plastic items. In 2021, the EU banned several plastic products such as straws, cutlery, plates, and cotton buds. More ambitious goals are on the way as part of the EU Green Deal and Packaging and Packaging Waste Regulation (PPWR) revisions, which aim to make all packaging reusable or recyclable by 2030.
The EU’s Push for Sustainable Packaging Innovation
The EIB’s investment in PulPac is not just a one-off. It reflects a broader European commitment to innovative, scalable alternatives to plastic that can support climate goals, reduce pollution, and boost industrial competitiveness.
“By supporting PulPac, we are backing an innovative and scalable solution that can make a real difference in the global effort to reduce plastic waste and accelerate the green transition,” said Thomas Östros, EIB Vice President, in a press release.
This is part of the EU’s InvestEU initiative, which mobilizes public and private capital to meet key policy objectives, including climate neutrality, digitalization, and industrial sovereignty. PulPac’s solution hits several of these targets at once—green tech, circularity, and sustainable industrial scaling.
Use Cases: Rigid Packaging That Outperforms Plastic
PulPac’s technology is best suited for rigid packaging applications—products like:
- Coffee cup lids
- Fast food trays and plates
- Single-use cutlery
- Personal care pods
- Fashion hangers
- Pharmaceutical and medical packaging
These are areas where plastic is still widely used and often difficult to recycle. With Dry Molded Fiber, brands can swap in a renewable, recyclable, and compostable alternative without sacrificing performance—or profitability.
Sundell notes that scalability is key to the company’s long-term vision.
“Over the next three to five years, we aim to become the global standard for scalable fiber packaging by providing a conscious solution with cost efficiency and consumer convenience without compromise.”
What’s Next for PulPac?
The EIB’s €20 million investment gives PulPac the firepower to expand R&D and optimize the cost-performance of its next-generation packaging. It also helps the company support its growing network of partners across the globe.
More funding rounds or strategic partnerships may follow as demand grows. But with regulations tightening, consumer expectations rising, and brand owners under pressure to act, PulPac could be in a prime position to deliver.